Liquid filling is an art!
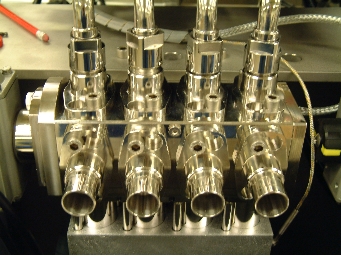
Liquid filling process, an art?
Does that mean the pattern of the spills then?
If you've tried filling bottles of shampoo at one hundred and twenty bottles a minute! You may be forgiven for thinking "that's gonna be messy".
Point of fact is, it probably would be, very messy without a machine. An inline or rotary liquid filling machine.
A purpose made filling machine not only fit for the job, but very good at it.
So let's have a little look-see as to how it's done without making a mess shall we then.
By the way, don't you think that nice shiny valve block looks artistic? Modern art maybe.
Yes ok, they are nice and shiny! All the magpie's amongst us will appreciate that. But they how they perform is the art form we're looking at here.
Right, let's kick off with a bit of general background first, yeah!
Now, believe it or not one of the most bubbly products to fill a bottle, or container with, is in fact, water!
Yes! Sounds surprising doesn't it, but that's quite true.
The single most biggest problem with liquid filling is actually air. You can't have bubbles without it. Sounds obvious I know, liquids do not compress, but air is very elastic.
Mix a little air with anything being expelled under pressure and you'll get loads of bubbles or foaming as the pro's call it.
Then if you were to add a little soapiness into this liquid filling equation,
yeah you get the picture!
A BUBBLE MONSTER!!!
(Foam monster doesn't sound as good, ha ha)
This foaming effect is a liquid filling nightmare, you might say!
So the aim of any liquid filling machine system has to, at the very least, be keeping air out of the filling process.
This is fairly easy within the pipes and valves on the machine. Well in as much as all the joints have to be a perfect seal!
But what about where the liquid exits (squirts, spays or splatters) the filling tube, (called a nozzle) into the bottle being filled. That has to be an air gap, right!
You would think that's true, as all batch machine processes have to allow room under the nozzle(s). This is of course for full bottles or containers to be removed and empty ones inserted.
Also, by the same token with inline and rotary machine processes, full bottles are swapped out for the next lot of empty ones as an ongoing process. So we have an air gap at the point of filling then, right?
Well, err, right and wrong actually!
It depends on how the bottle or container in question is actually being filled.
So ladies and gentlemen, without further ado, let me introduce;
The Diving Nozzle! Ta daaa!
The diving nozzle really lives up to its name, as it can dive right down into the bottle. Right to the bottom if needed, hmmm a clever little devil of a nozzle.
Now, this clever little devil nozzle operation, overcomes the problems encountered when filling foamy products. With a diving nozzle assembly incorporated, this allows the filling nozzle(s) to dive right to the bottom of the bottle or container.
The bottle (or container) is then filled with the nozzle(s) rising just under the rising liquid. This practically guarantees a lovely smooth filling process as the foaming is virtually eliminated by the nozzle outlet being submerged.
The bonus of course is, allowing for greatly increased production outputs, on what would otherwise be a relatively slow liquid filling process.
But, the diving nozzle is not a new idea!
Having the ol' diving nozzle action allows for several different filling methods to be used. In addition to the basic top filling method, which is the most obvious I would think.
There are several recognized methods within the liquid filling world. There's top fill, bottom fill, bottom up fill, side fill and vacuum fill just about covers the main groups of methods used.
Of course, there are a number of variations within these groups, such as spray fill and rotary fill to name a couple. Which method and/or variant is used, really boils down to the nature of the product to be put into bottles.
Perhaps the shape of your bottles or containers is limiting your liquid filling speeds? Most bottles/containers tend to narrow towards the neck.
Some more than others.
This can cause the actual product being filled by the liquid filling machine to get in the way of the displaced air escaping when filling at speed.
Sooooo... the result is SPLAT.
The liquid product spurting out of the neck and probably over you and on the floor! Either way some is wasted.
In this situation the vacuum filling operation would be a perfect solution (solution - liquid filling...get it) to the problem of squirt splat.
Of course having said that I really ought to say also that vacuum liquid filling is only suited to free flowing liquids. Like alcohol solution for perfumes, white spirit and other thin clear (no bits) solutions.
So, while we're on the subject of splats!
Drip, drip, drip, how do you stop that.
To overcome liquid filling equipment from giving "dripping" problems, just takes years of experience I'm afraid.
Only the experience in test filling thousands of liquids enables the development of a vast range of different filling nozzles. This experience is what makes it possible to solve a lot of the problems of dripping and stringing.
For stringy products, like some shampoos and liquid soaps, a suck back system will give you a quick, smooth drip free fill. With the suitable nozzle of course.
The suck back system is another name sake, at the end of fill the liquid is sucked back a slight bit to remove any excess from the nozzle tip. The nozzle would be designed for this system.
Valves:
At this point, you should know that liquid filling machines divide liquids into two categories. Those with bits and those without.
"Bits! What do I mean by bits?"
Ahh now I'm glad you asked that. Bits is the industry standard (nick) name for any liquid with particles, lumps, solid or grains. A classic example is the mechanic or engineers hand cleaner with the grains in for deep cleaning dirty hands.
Any liquid product with bits in it absolutely must use a filling machine equipped with a rotary outputting valve.
"Why's that?" I hear you say!
Simple, nearly all liquid filling machines use valves. Rotary, gate, ball & spring and poppet valves. All of these valves with the only exception being the rotary, can be prevented from sealing correctly by...
Yeah, you got it, BITS!
No seal, no work!!!
Trust me on this one. If this rule is not taken seriously, you will get no end of hassle with your filling machine. Inaccuracies of filling levels and poor machine operation due to sticking valves and/or valve just not being able to close properly to seal.
"Are rotary valve liquid filling machines more expensive?"
Yes, they do cost a bit more, but not a huge amount. In any case, it's really not worth even trying to save a buck or two here.
It would be like trying to use a sieve as a bucket for fetching water, it just don't work.
This one, featured at the top of the page, is a four way 90 degrees rotary valve block, pneumatically operated.
Ya know, just in case you were wondering. Oh yes, there's my pencil.
Power:
Ok, so what powers a liquid filling machine and how much of that power does it need to operate?
Hmmm that's a good point with not a straight answer.
No I didn't say I wouldn't answer, I can answer that one very well if you'll allow me some indulgence here. There is no straight answer to this one because there are so many different types of liquid filling machines available.
Liquid filling machines range from the humble little single nozzle, hand cranked, bench mounted filling machine. All the way up to a fully automated multi-head high speed rotary filler/capper.
Each of these many different types of machines are suited to a particular type of filling job, but they all use an amount of power. Of course, power could mean electric, pneumatic, mechanical and even hydraulic, although that is a rare case.
Or a combination of any or all of the forms of power could be used in the operation of a single liquid filling machine.
So, what about the humble hand cranked bench mounted filling machine.
What power does that use?
Human power of course, although this type of beastie will normally have a two or three foot handle to pump with to make the most of the lever effect. Builds your arms up nicely even then.
Electrical power is by far the most common for powering any machine not just the liquid filling variety. How much of it is used by the machine depends on several things.
Heating takes quite a bit of power as does lifting heavy things, liquids can work out to be quite heavy if lifting or moving a large amount of it at one time.
Heating of some type products is essential for liquid filling as after filling and cooling, the product sets solid. For example, did you know that the underarm deodorant stick is actually filled hot as a liquid at around 65 degrees?
The filled containers are usually then sent slowly through a huge fridge called a chiller. The chiller takes the form of quite a large room sized box with a conveyor across the width of it's floor. On which the filled containers move across in their hundreds. Cooling down as they go.
But having said that, a gravity fed liquid filling machine, fed from a hopper above the dispensing point. With a product filled at room temperature would be able to operate from a normal 13A domestic socket.
It would, I suspect need a compressed air supply too, but if designed correctly would not use a great deal of air. The air supply in this case would be just to operate the rotary valves and cylinders to make the machine work.
A liquid filling machine can be designed to be quite power conscious indeed if the product is to be filled into bottles at room temperature.
The only lifting would be to get it into the supply hopper to start with. This could also be done quite efficiently with a general fluid pump, or a bucket and ladder if you're the energetic type.
But that really would be your personal call, I don't know of any hopper filling services, ha ha.
Control:
So we know what powers a liquid filling machine and how much of that power it needs to operate. As a general guide anyway, as we also know it depends a lot on the product in question?
But what is it that makes a liquid filling machine operate?
Some machines are completely operated by compressed air, some by hard wired relay circuits. Some by a good strong arm, well after a while it'll be strong!
But without a doubt, most semi-automatic or fully automatic liquid filling machines will have our little friend inside. The humble PLC.
A PLC is just about the most efficient method of control for any machine not just liquid filling machines.
For the smaller or semi automatic liquid filling machines some may consider a PLC a bit overboard. But I would oppose this point of view, if nothing else it would make changes in operation very easy.
Also with the addition of a small HMI and a well written program. (That's not too difficult for anyone into PLC programming and a lot of technicians and service engineers are).
The machine would be very versatile indeed as the operator would then be able to control the exact switching point of valves, solenoids and actuators. In doing so would be able to hone the operation of said machine to perfection!
After all operational efficiency is what this is all about, so that's got to be worth doing.
Inline or Rotary:
Righty ho; lets have a good ole' dig through at the differences between these two types of machine. Each of then has a specific position to fill,
(ha ha excuse the pun).
While both perform a very similar job, how the inline and rotary machines separately go about each of their job is quite different.
Let's have a scan through the pro's and con's for the inline and rotary fillers battle for supremacy.
Setting up:
Inline filling machines are very good at change!
"WHAT!"
Oh yes, what I mean is they are very versatile, an inline filler can be easily changed/setup to suit many a different size and shape of container.
This cannot be done so readily with a rotary filler, as a set of change parts have to be made for the machine with each different shape and/or size of container.
But because the rotary machine is made to run one size of container at one time it can usually do it at a faster pace than an inline machine. Also the setup time may be quicker as the rotary machine is setup simply by removing the current change parts and fitting the new set.
The change parts are normally three types of wheels specially shaped to the bottle being filled and an infeed spiral.
With the inline machine, each stop and photocell has to be repositioned to suit the new size container, as well as nozzles and neck locator's.
This is of course the very essence that makes the inline machine so versatile and adaptable. Couple this versatility to no change parts to re-manufacture every time a new bottle or container is introduced.
You will then have a very useful and don't forget, cheap to run machine indeed. A 12 head inline filling machine can be setup to keep pace with a rotary filler but the rotary will have the edge.
The rotary liquid filling machine has cost a lot more for the initial setup of just the one container, so make it worth while you better be running lots of 'em!
It's worth noting that the choice of inline or rotary machine is very much a case of horses for courses.
Although, unless your specific production demands are solely of a single type of container in high volumes. I personally would recommend the option of an inline liquid filling machine to fulfill most production demands.
As most productions demands are subject to change, it would be advantageous to be equipped to change with it. Cheaply and efficiently.
Go from Liquid Filling back to Machine 'In the Box'.
Return from Liquid Filling to Home.
ARE YOU TIRED OF RISING FUEL PRICES!!!
You Are Secure!
Enjoy this page? Please pay it forward. Here's how...
Would you prefer to share this page with others by linking to it?
- Click on the HTML link code below.
- Copy and paste it, adding a note of your own, into your blog, a Web page, forums, a blog comment,
your Facebook account, or anywhere that someone would find this page valuable.